

The software performs the particle size distribution in 2D in accordance with individual specifications. From outside of the conveyor belt edges, no image information is channelled into the computations.įine particles that are too small and below the resolution of the screen are assigned to the fines. Belt sections on which no material is conveyed are identified by the software as “empty” and are not included in the analysis process (Fig. 3). In the image processing, first optical transmission weaknesses are compensated for by means of filters, and contrast corrections are automatically performed, before the software starts with the analytical segmentation. The advantage of the software is the precise analysis of the video stream delivered by the camera, from which up to ten images per second can extracted and analysed (Fig. 2).
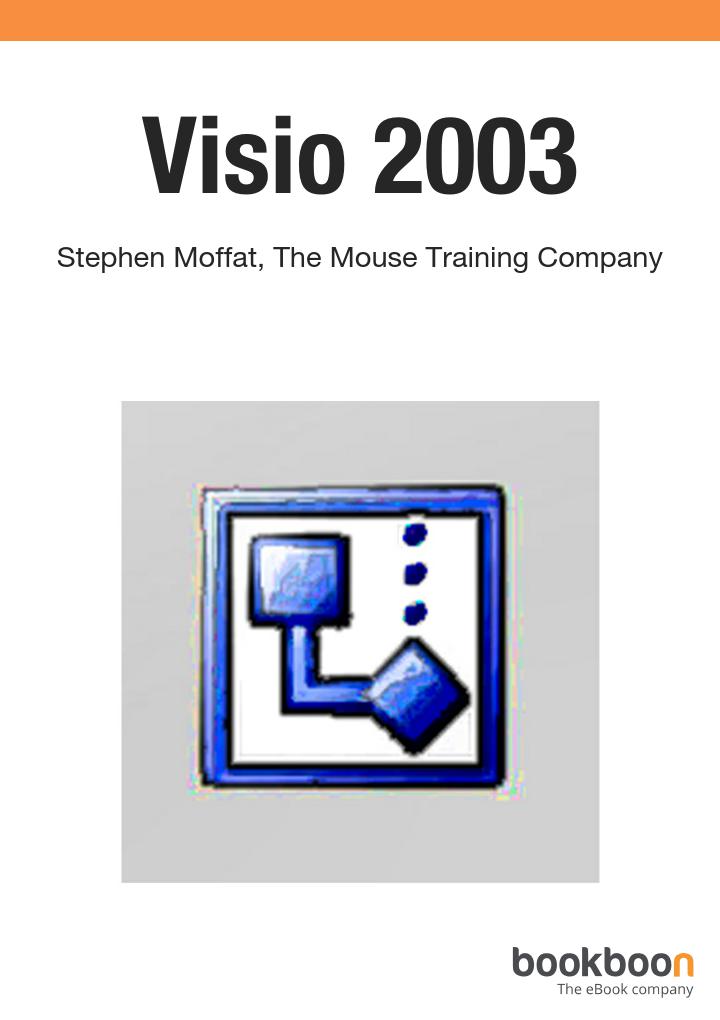
The VisioRock™ software can be administrated from a normal PC interface, can be integrated in an OPC server and TCP/IP in LAN and WAN structures and is usually operated from the control room. When fitting the camera, it is necessary to make sure that the lens is shielded against scattered light – especially as a large number of conveyors are installed outdoors. The camera itself is fitted with a dust protection system that can be optionally connected to an air compressor. The hardware is installed above the conveyor. The VisioRock™ process monitoring system includes a video (IP-) network camera in a stainless steel casing (protection rating IP67) together with LED lighting and set-up equipment. Size, colour, texture and particle shape of the rock can be analysed. Especially in mills, adjustment of the suitable feed rate is directly connected with the particle size.
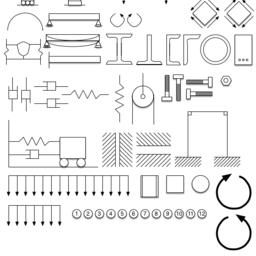

The system combines dependable particle size measurement with the possibility to directly adjust the crusher gap setting if any deviation from specifications is detected. At the focus of interest is the feed material for different crushing stages or mills. With VisioRock™, the visual process monitoring system from Metso, it is possible to monitor and analyse visible rock particles in the production process (Fig. 1). To obtain greater transparency in mineral processing and more accurate information on size distribution in the feed and discharge of crushing processes, reliable monitors are needed.
